The Moulding
Process
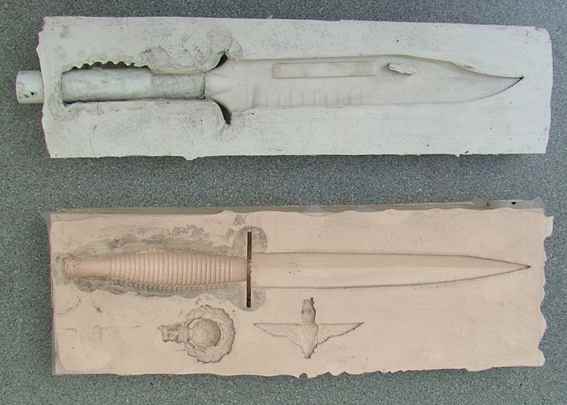
First the impression is made
of the item. As you can see above we have made 2
impressions - an SA80 Bayonet and a Fairbairn Sykes
Commando Dagger. A Royal Marine and The Parachute
Regiment capbadges have also been used. The two
blocks you can see are made of silicone rubber, and
are therefore reusable. Each mould is thoroughly
cleaned prior to casting. A removable bung is added
to the Bayonet to ensure the handle is hollow.
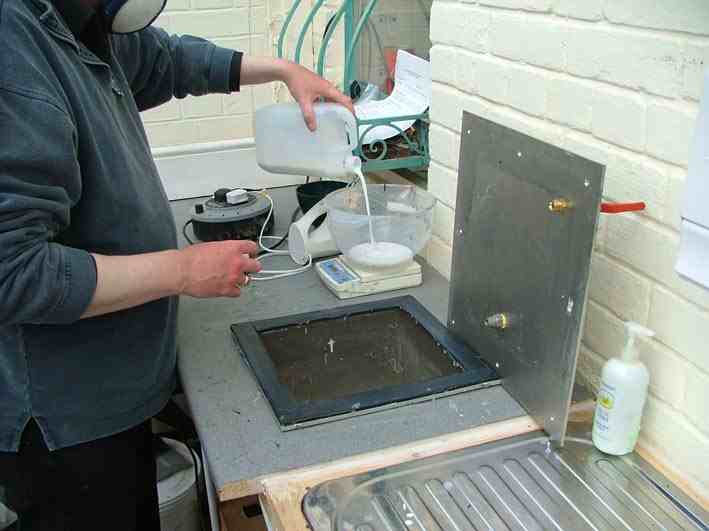
Next we measure
out our acrylic resin. This is made up of two parts
- a liquid and a dry powder. The resin is non toxic
and is environmentally friendly. The resin we use
has been specifically identified a it produces a
high definition of the original impression. As you
can see our technician isn't wearing gloves. He is
wearing a mask, but purely to protect him from
breathing in the powder you can see in the next
picture.
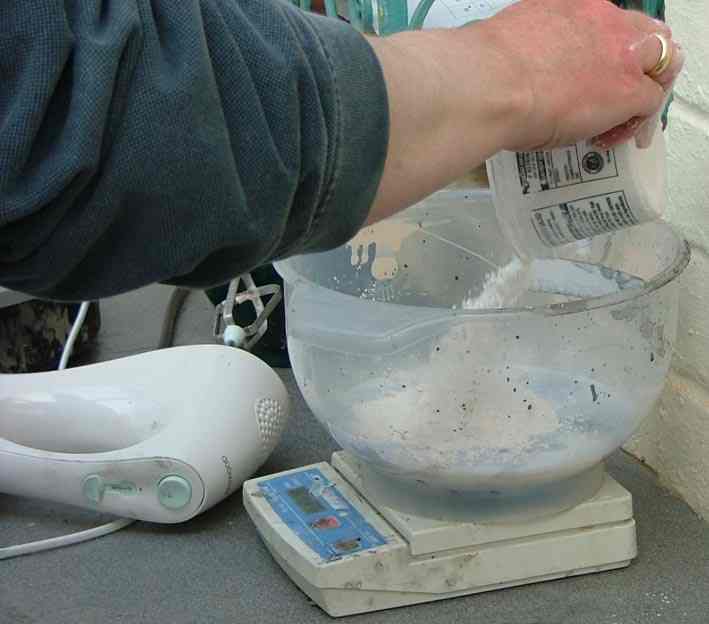
A colourant is
then added (not pictured), and the whole mixture is
then placed in our vacuum chamber and is worked to
ensure the resin thoroughly mixed. As soon as the
two elements are added together, a chemical reaction
commences whereby the mixture begins to heat up and
begins to set. The mixture is useable for around 10
minutes, depending on room temperature before is
goes solid.
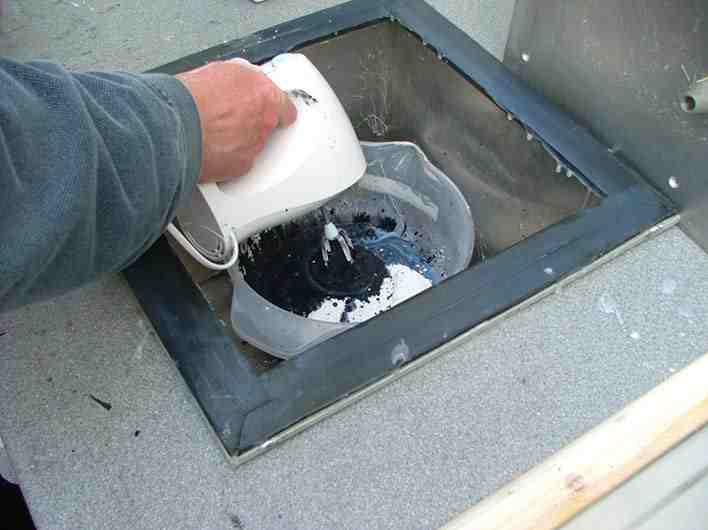
The lid is then
placed on the vacuum chamber, and air is sucked out
until the atmosphere is equal to 1. The reason for
doing this is to remove all air bubbles that are
produced when mixing from the mixture. This step is
repeated twice.
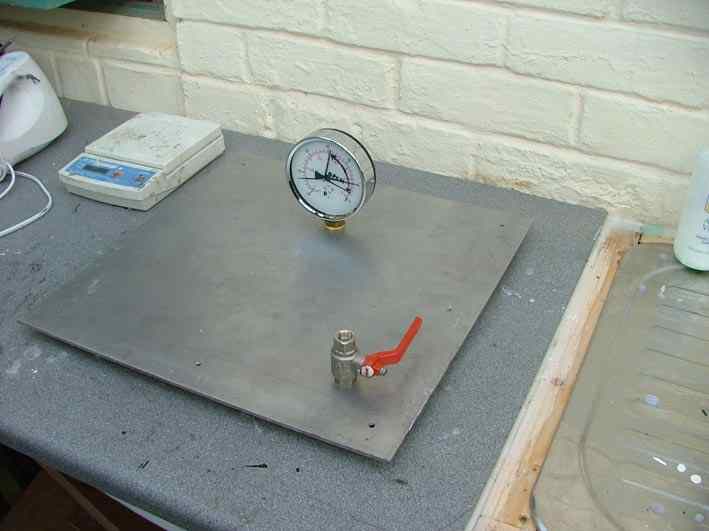
The liquid is
then carefully removed from the chamber, and is
slowly poured into the moulds.
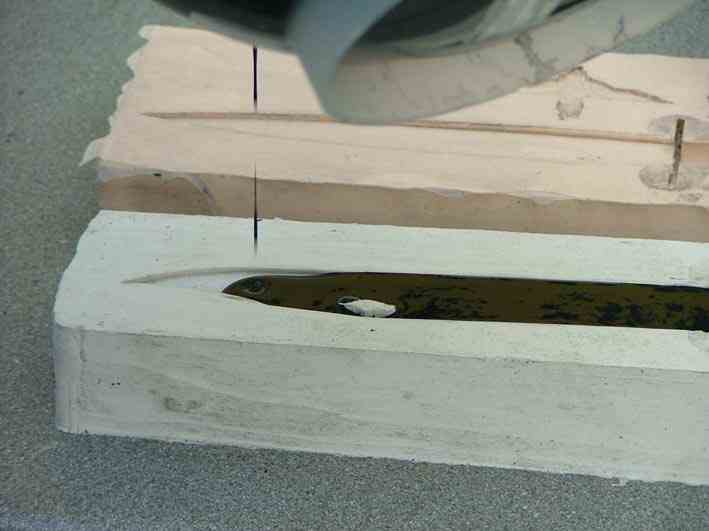

After 24 hours
the casts are removed from the moulds before being
painted and mounted on fabric in frames.
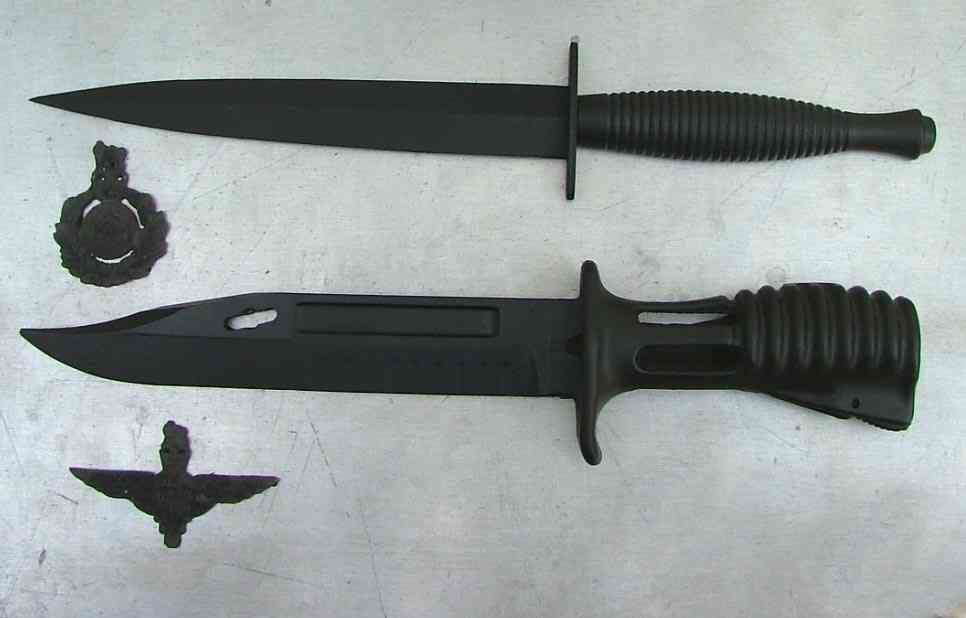
The finished
product has a low toxicity and in these days of
heighten security are designed to break if any
attempt is made to removed them from the frame. As a
replica, the moulding is only a half impression of
the original item.